Monro Contracting has constructed a series of stormwater retention ponds for the Christchurch City Council over the past two years. The ponds are at the base of Christchurch’s Port Hills in Tai Tapu, at the back of the former Halswell Quarry. The ponds are intended to catch the surface runoff from a developed area nearby and almost 100 hectares of the surrounding hillside. These ponds aim to reduce the effects of flooding in the low-lying farmland and control the water runoff rate into the nearby Halswell River. The ponds will also support future residential development. Matt and Peter Monro from Monro Contracting contacted Terra Cat for advice about compaction control and monitoring systems. Monro Contracting wanted a real-time compaction monitoring system to indicate when they had achieved the desired soil density without under-compacting or unnecessary over-compaction. They wanted to record these results for analysis and quality control. The goals of using the technology were:
Provide sufficient compaction to achieve the project’s specified density and moisture content targets
Optimise machine utilisation to reduce unnecessary fuel burn and construction time
Provide the operator with real-time monitoring of compaction effort and coverage
Ensure optimum compaction coverage with no missing areas or gaps
Archive compaction data
Reduce the frequency of soil testing
After some discussion and considering the soil on-site, its prescribed treatment, construction methodology and soil testing regime. The recommended solution consisted of:
A CS56B soil compactor with sheepsfoot shells to compact the cohesive lime-treated soil using both vibratory and static modes supplied by Cat Rental
The use of factory-fitted Caterpillar Machine Drive Power (MDP) technology to measure the soil stiffness of the cohesive material
A factory fit high accuracy Trimble RTK GNSS system and Trimble Works Manager software supplied by Sitech to map and record position and elevation data
What is MDP?
Caterpillar’s MDP system is a way for soil compactors to measure the stiffness of soil. When a soil compactor drives over a material’s surface, it produces a bow wave of material in front of the drum. As the ground stiffens due to compaction, the resistance from the bow wave of material is reduced. With each pass, the drum requires less energy and machine drive power to turn and overcome this resistance.
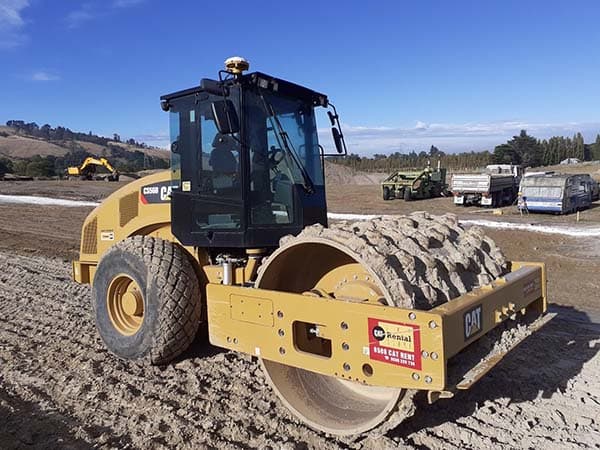
Advantages of MDP
MDP has several advantages over other on-machine, accelerometer-based soil compaction measuring techniques that made it ideal for this project:
Contractors can use it on granular and cohesive soil types
Contractors can use it in both vibratory and static rolling modes
It measures soil stiffness between 300mm and 600mm below the surface
The Project Prescription
The project’s engineers prescribed that each lift would have additional lime and water added to the Port Hills loess. The soil was mixed to a loose depth of 200mm before compacting using a combination of vibratory and static passes.
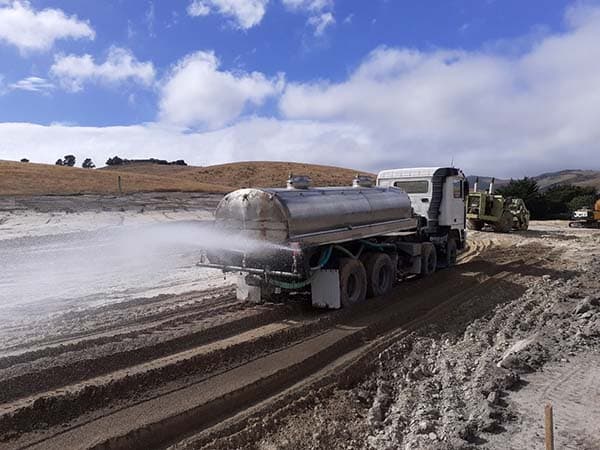
Monro then conducted a construction trial to find the right soil treatment procedures and rolling pattern per lift to reach the target Optimum Moisture Content (OMC) and Maximum Dry Density (MDD) percentages set by the laboratory. The site engineers did on-site soil testing with a nuclear densometer, and post-construction soil samples were also sent back to the laboratory for further verification.
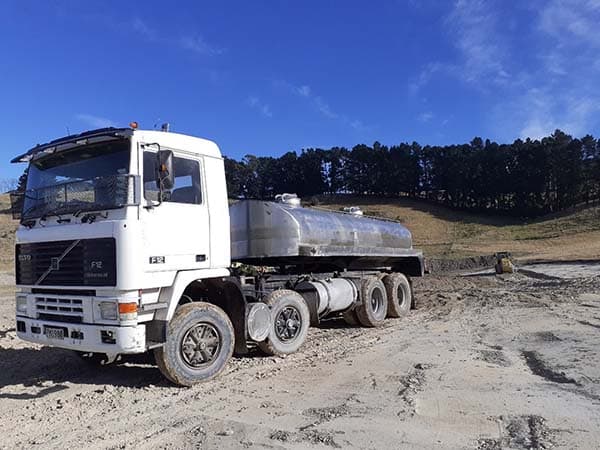
Results
In-situ soil testing with the nuclear densometer showed an increase in OMC and MDD with each compactor pass. Real-time monitoring in the machine also showed a steady increase in MDP values with each pass.
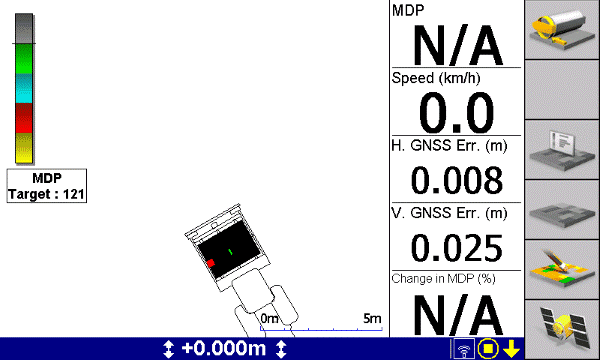
Continued construction and testing eventually showed a plateauing in results with the nuclear densometer and MDP values. This plateauing of results was further reinforced by the consistent number of pass counts needed to achieve these results.
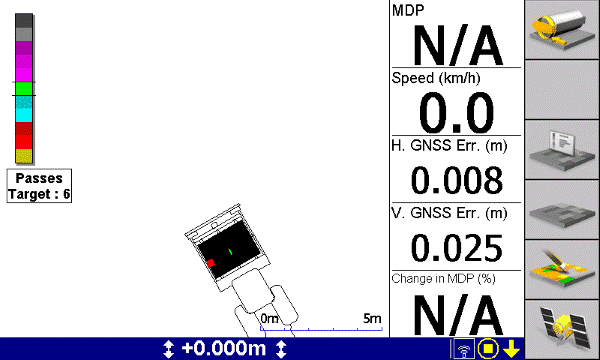
The Benefits of Using MDP
From this construction trial, a target MDP value and number of passes were obtained by Monro Contracting as:
Using this target MDP would give Monro Contracting confidence they would achieve their target OMC and MDD percentages
Using a pass count target meant they could optimise machine utilisation, reducing fuel burn, machine hours and construction time
Realtime monitoring in the cab meant the operator could identify problem areas as they arose. Using the machine’s GNSS mapping ensured that compaction coverage was consistent across the entire work area with no gaps.
Peter Monro explains, “We found the system very helpful, having the MDP value on-screen meant the operator knew when the target MDP value was met and the corresponding nuclear densometer test would verify the target OMC and MDD values were being met. This also meant ultimately lower machine operating hours and fuel burn. Having the 3D mapping on-screen also meant the operator could ensure he was covering the entire area and not missing any areas.” Pass counts are the most common method of compaction control today. MDP offers a way to potentially optimise compactive effort and machine utilisation, while at the same time achieving and maintaining target densities without the need for repetitive and intensive soil testing using a nuclear densometer. When combined with a high-accuracy GNSS mapping system, the contractor can ensure compaction coverage, while recording position and MDP data can be stored by Monro Contracting for quality analysis and archiving.
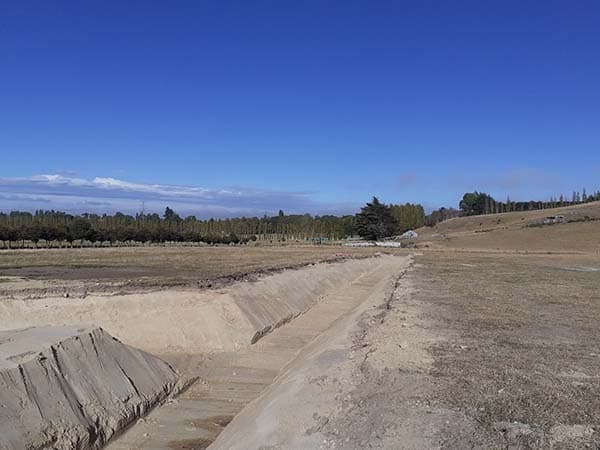