The first Next Generation models in Caterpillar’s compact track loader line, the Cat® 255 and 265 are ground-up redesigns of their predecessors. Shaped by feedback from the operators who run them day-to-day, these models offer powerful performance, a better in-cab experience and a suite of industry-leading upgrades, which make all the difference for customers like Manawatū-based Stringfellow Contracts Ltd.
Building on the features that made the D3 series so popular, the Next Gen 255 and 265 elevate Caterpillar’s loader reputation through improved engine performance, lift and tilt breakout force, stability, operator comfort and technology.
Compared to the 259D3, the 255 offers a class-leading lift height of 3.15 metres, 36% more tilt and 26% more lift breakout force, while the 265 tops out 3.35 metres and improves on the 289D3 with 19% more tilt and 22% more lift breakout force.
Powered by Cat C2.8T and Cat C2.8TA engines respectively, both deliver 74.3 hp (55.4 kW), maintain horsepower across a wider RPM range and boast significant torque increases – that’s a gain of 13% for the 255 and 43% for the 265.
Standard hydraulic system pressure is increased to 3,500 psi (24,130 kPa), meaning the loaders support all Cat Smart Attachments with the standard auxiliary hydraulics. Terra Cat industry manager Tim O'Meara explains that the ability to activate High Flow functionality via software is also new for these Next Generation machines.
“Both models are factory fitted as ‘high flow ready’, so if in the future you’d like to attach a high-performance work tool, High Flow functionality can be activated when and where you need it.”
A redesigned engine compartment that mounts the engine and cooling package lower into the frame and a stronger, stiffer undercarriage with torsion bar suspension mean the loaders deliver improved stability, load handling, material retention, and a smoother finish when grading.
But don’t take it from us. Among the first to put the Cat 265 to work in New Zealand is Manawatū-based Stringfellow Contracts Ltd., a team with over 50 years in business and a portfolio spanning earthworks, drainage, roading, infrastructure and more.
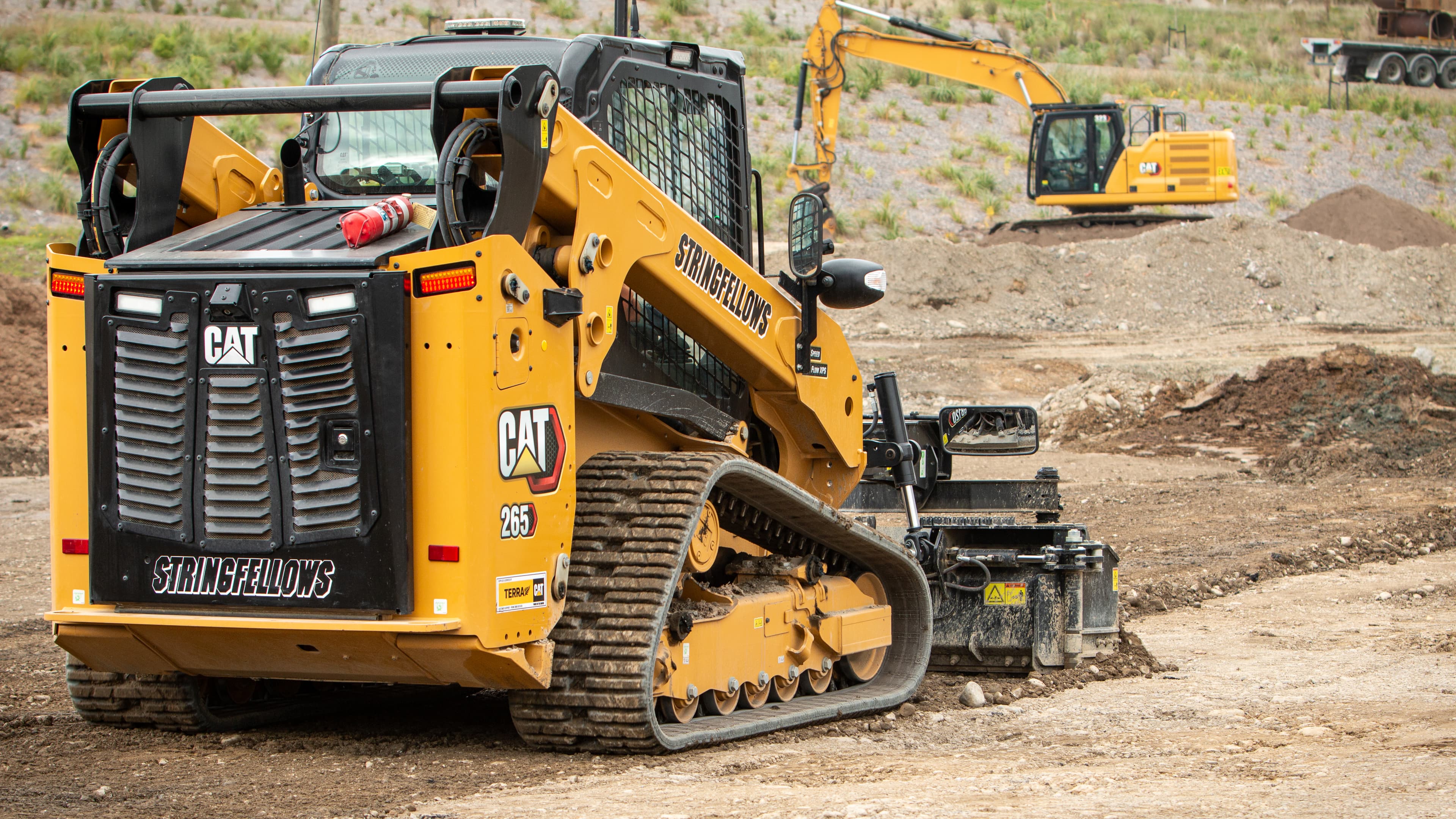
According to Stringfellows’ general manager, Simon de Rose, the 265 slotted into their operation exactly as intended.
“We had a specific application in mind – we were looking for a suitably sized machine for kerb and channel preparation which had the technology and the attachments to handle the whole job without the need for handwork,” says Simon.
“With the kind of technology integrated into that machine, and the grader blade attachment we picked up with it, it’s hit the brief exactly. We have been able to complete the same task a lot quicker, and with a more precise finish.”
Featuring a low entry point, entering and exiting the 255 and 265 loaders is easier than ever before. The redesign allows the operator to open the cab door without fully lowering lift arms to the frame stops. Visibility is also improved as a result of the lower engine mounting, with a 59% larger rear window and a bigger top window that provides a 15% increase in viewable area.
“The standout was definitely the space in the cab,” says Simon. “That, plus all the upgrades made to the interior – it’s a much more enjoyable environment for the guys working in it day-to-day”.
These ‘upgrades’ include a host of changes to the cab design and technology. Inside the cab, both the 255 and 265 offer 22% more volume and 26% additional foot space, with increased interior width, height, and hip room. The improved HVAC system now features auto temperature control, and operators have a range of mechanical and air-ride suspension seat options to choose from.
The loaders also come with either a 127mm LCD monitor or a 203mm advanced touchscreen. The standard monitor supports Bluetooth, a rearview camera feed, creep, job clock, and maintenance reminders, while the advanced touchscreen provides additional control, including a multicamera 270˚ view. Redesigned joysticks allow the operator to control all machine functions without removing their hands from the controls, and the unsurprisingly popular X-grip smartphone holder keeps their devices secure.
“All those in-cab features make such a difference,” says Tim O’Meara. “That’s been a big motivation behind the demo days we’ve held across the country over the last few months.
“It’s about getting operators into the new machines to experience those improvements firsthand – and to see how the performance upgrades can transform a jobsite.”
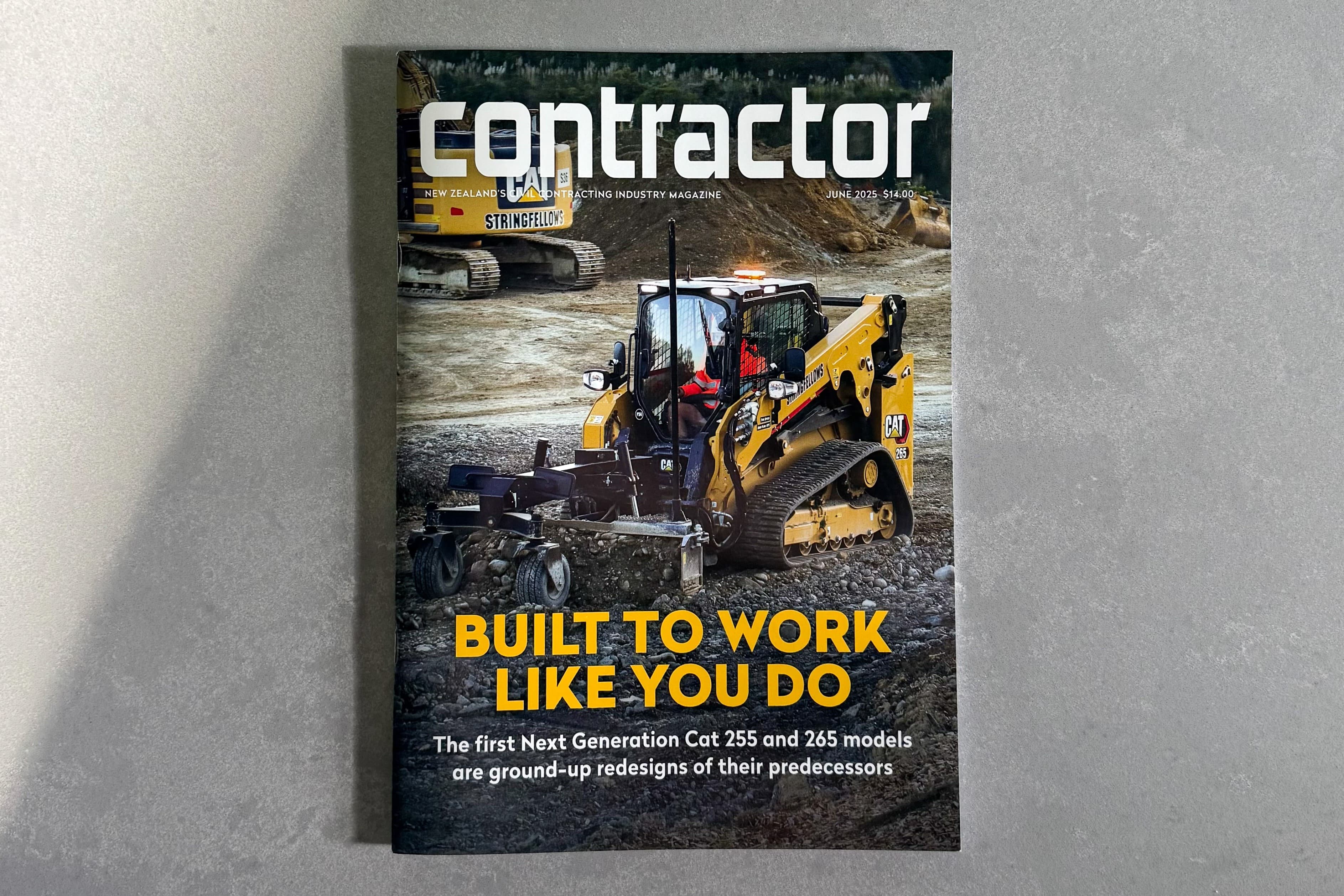
This article was first published in the June 2025 issue of Contractor.